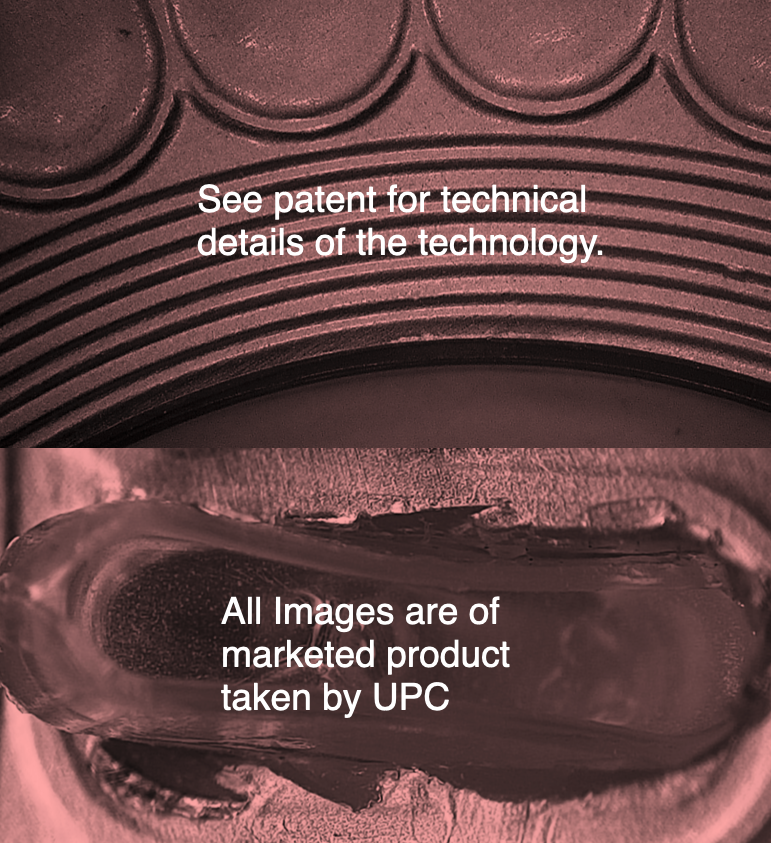
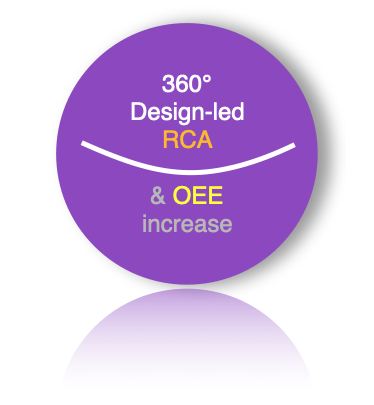
Foil Critical to Quality (CtQ)
The UPC customer wished to know from first-principles what differing processes affected the foiling integrity carried out at a different location.
A number of different tool suite IQ, OQ and PQ retains were retrieved from storage and delivered to the UPC Laboratory.
The first sessions were used to decided which area of the mouldings were possibly not perfect, and thus would cause imperfect foiling downstream.
Next various metrology methods were trialled to find the optimum and most cost-efficient way to generate data. Over a three week period 33,000 data points were generated at UPC; Analysed, graphed and cross-compared.
The answers to ‘how does this process work’ were clear, as were ‘what measurements need to be controlled and to what tolerance’.
A great result for our customer.
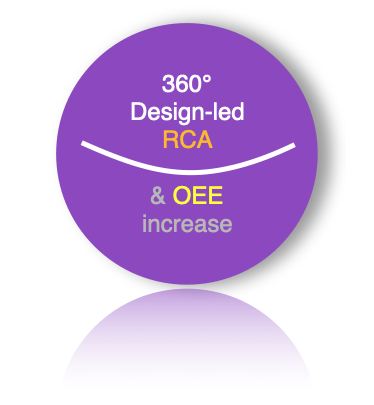
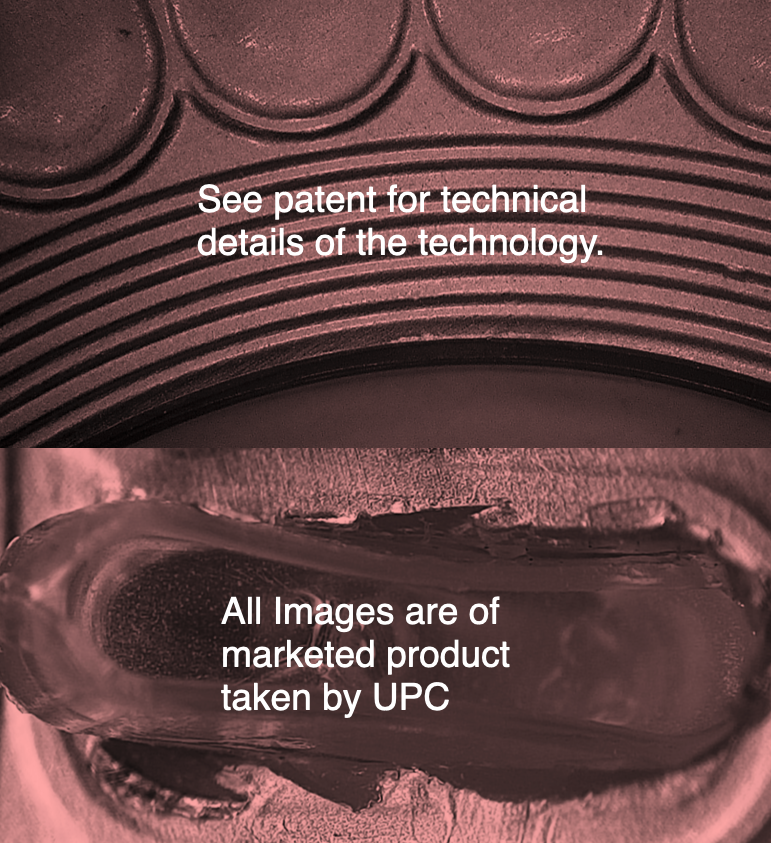
Foil Critical to Quality (CtQ)
The UPC customer wished to know from first-principles what differing processes affected the foiling integrity carried out at a different location.
A number of different tool suite IQ, OQ and PQ retains were retrieved from storage and delivered to the UPC Laboratory.
The first sessions were used to decided which area of the mouldings were possibly not perfect, and thus would cause imperfect foiling downstream.
Next various metrology methods were trialled to find the optimum and most cost-efficient way to generate data. Over a three week period 33,000 data points were generated at UPC; Analysed, graphed and cross-compared.
The answers to ‘how does this process work’ were clear, as were ‘what measurements need to be controlled and to what tolerance’.
A great result for our customer.
Manufacturing process design from first-principles.
The foiling process know-how and IPR belonged to another company, so UPC was instructed to generate it’s own ‘most-likely’ process by reverse engineering from inspection and measurement of marketed product.
We needed to find out what the foiling substrate flatness requirements were to achieve reliable bonding, and this is exactly what we did.
Further we trialled three different metrology QC methods for the substrate component and then cross-compared the data with the reject levels that were known.
It became clear that the simplest contact method was actually the most reliable and fastest at obtaining metrology data, and had the best correlation to reliable foiling.
Often you just need to know where and what to measure as an In Process Control (IPC).
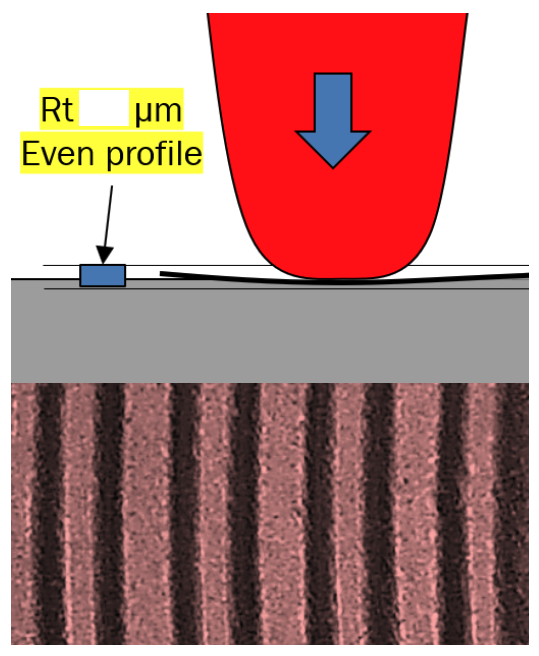
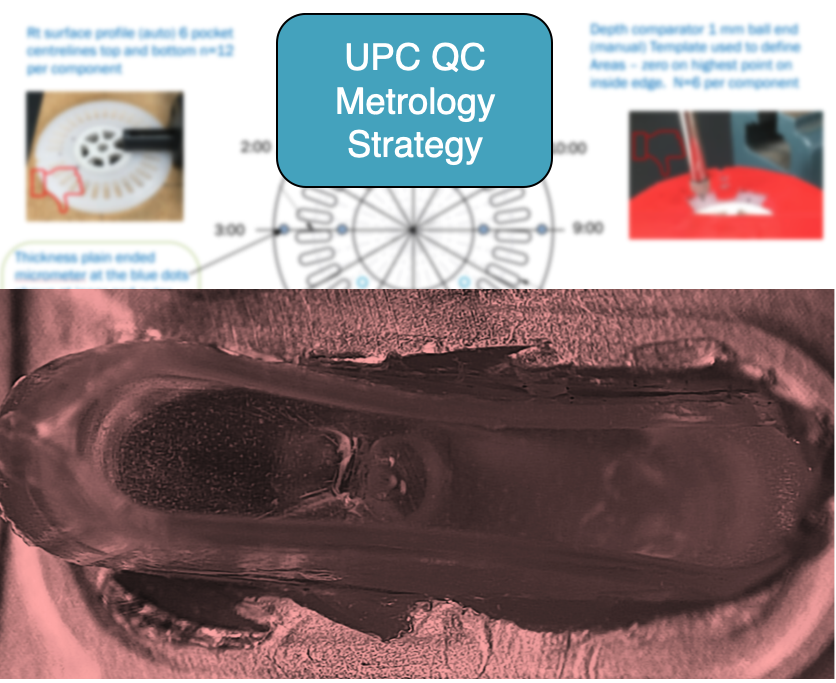
Good presentation is vital to enhance the message.
UPC is known for clear presentations, if somewhat detailed and lengthy at times.
However in this case the slide opposite, which is intentionally blurred, provided a one-page picture of the metrology strategy for this product.
We know that photographs and diagrams are required at all times to make the complex understandable and thus transferrable. This one leaps out as being excellent.
Root Cause Analysis is often taught as if a standard process can be applied to any problem, and the result will just become apparent. At UPC we have learnt that applying design for performance and design for manufacture and assembly, at the same time is what gets results.
The only drawback is that you need to be fairly expert to conduct ‘RCA by Design’, it is not for beginners.