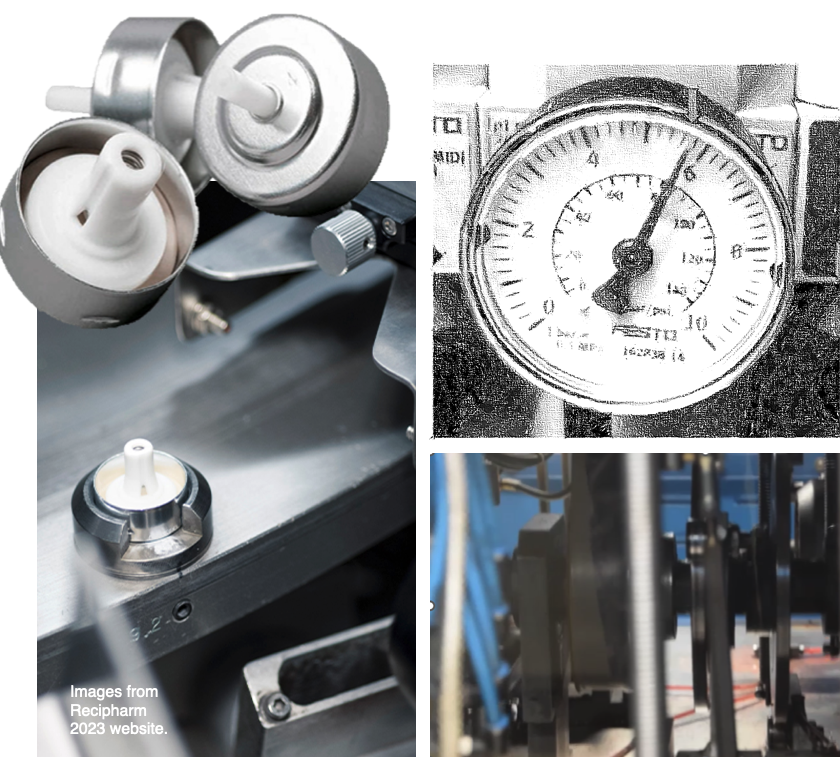
Automation and Product Design
UPC worked in collaboration with Recipharm to complete a systematic hands-on review of the manufacturing assets from a product design perspective, as well as from the automated assembly requirements.
Design & Manufacture need to work in harmony to:
- Meet design requirements at each station
- Reliably 100% pick and 100% place
- Reliably 100% test
- Achieve low reject levels at each station
- Optimise QC e.g vision systems
- Achieve low rejects at each machine output
After months of machine high speed video visits and other key measurements, refinements were implemented to give OEE near to 90% for the automats under review.
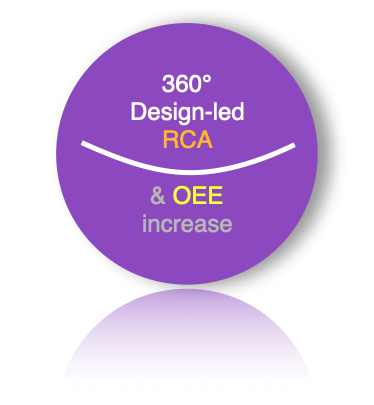
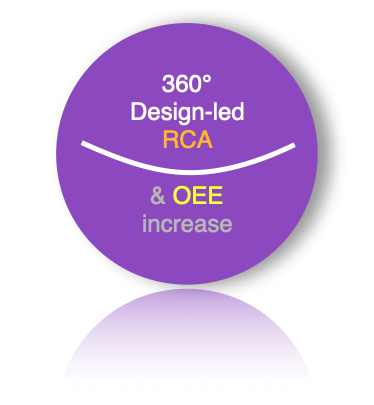
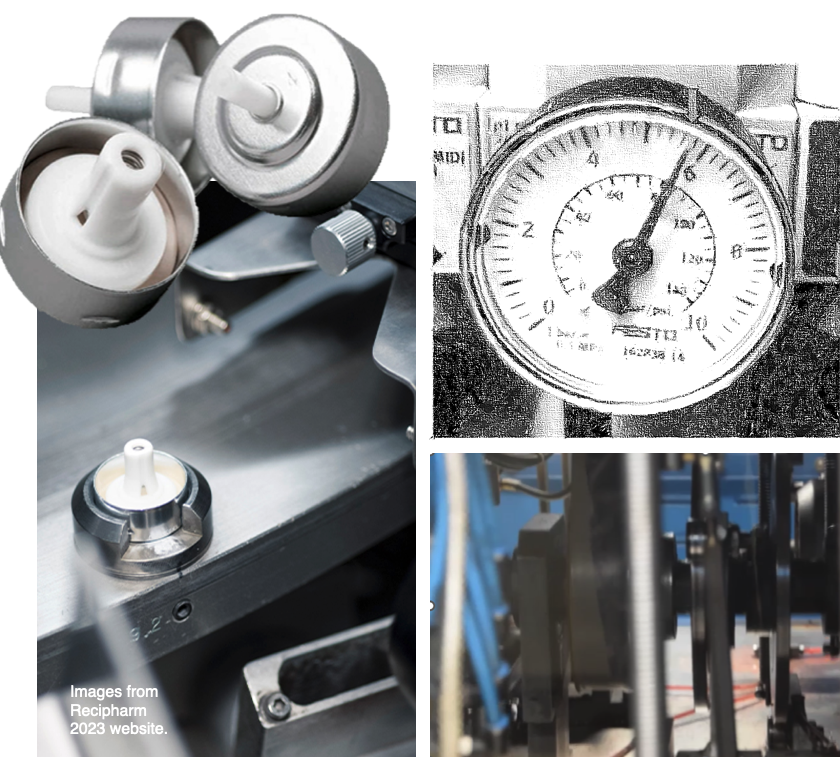
Automation and Product Design
UPC worked in collaboration with Recipharm to complete a systematic hands-on review of the manufacturing assets from a product design perspective, as well as from the automated assembly requirements.
Design & Manufacture need to work in harmony to:
- Meet design requirements at each station
- Reliably 100% pick and 100% place
- Reliably 100% test
- Achieve low reject levels at each station
- Optimise QC e.g vision systems
- Achieve low rejects at each machine output
After months of machine high speed video visits and other key measurements, refinements were implemented to give OEE near to 90% for the automats under review.
Data and more data from slow motion analysis and station reject counts
Using slow motion analysis the key moments of component pick and next place can be studied. Time consuming, but vital to ensure facts are understood, before change is implemented.
Tooling Contact Surface refinement both in terms of geometry and finish is critical to reliable performance with minimal effect on component and assembly performance.
UPC skill set enabled a holistic approach to be taken, from both a product design and automat design simultaneously.
In this way we were able to both champion the patient, as well as offer constructive improvement plans for the engineering team supporting a live product stream.
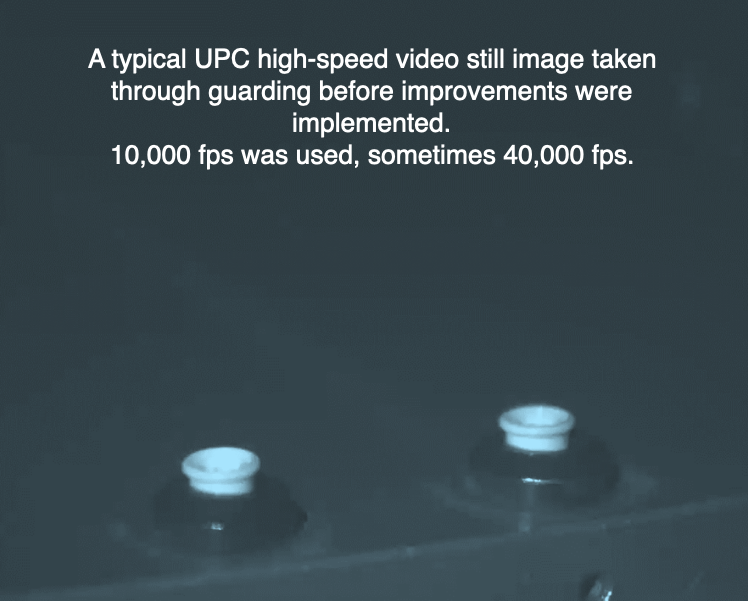
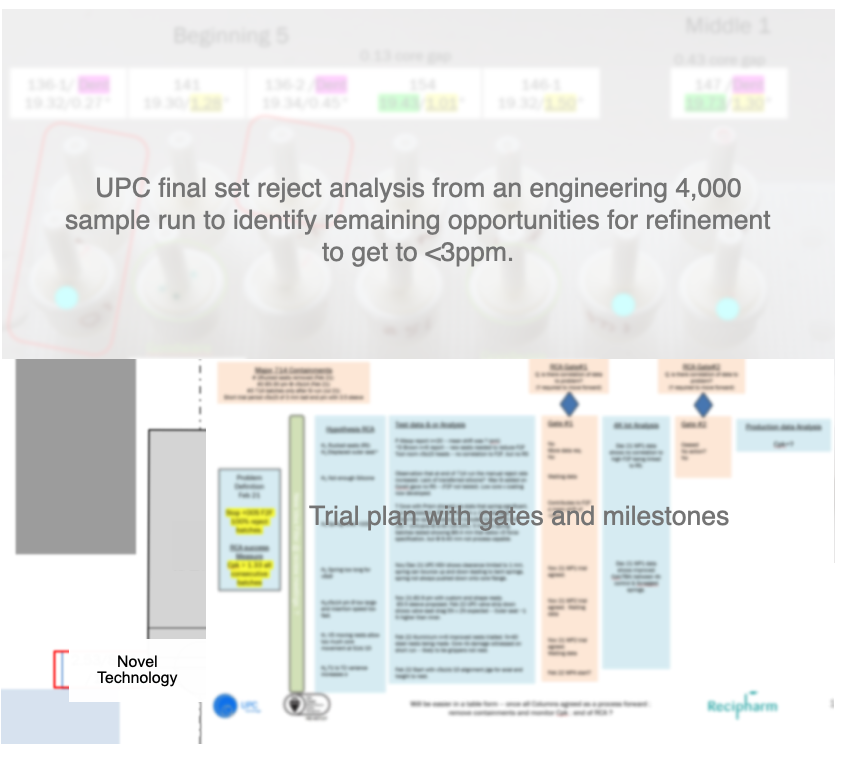
The reject bin is where key data and thus intelligence lies.
From three work packages assessed, one route provided the best gain for a modest investment in hardware by Recipharm.
As a truly collaborative Team effort we achieved:
- Quality metrics taken from below target to Cpk > 2.0
- Operating Equipment Efficiency driven up to ~90% per shift.
- Annual cost-savings made gave ROI in ~5 weeks.
‘An absolutely magnificent achievement’
UPC wish to repeat in future collaborations
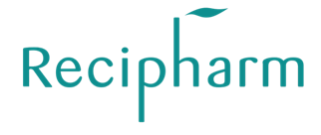