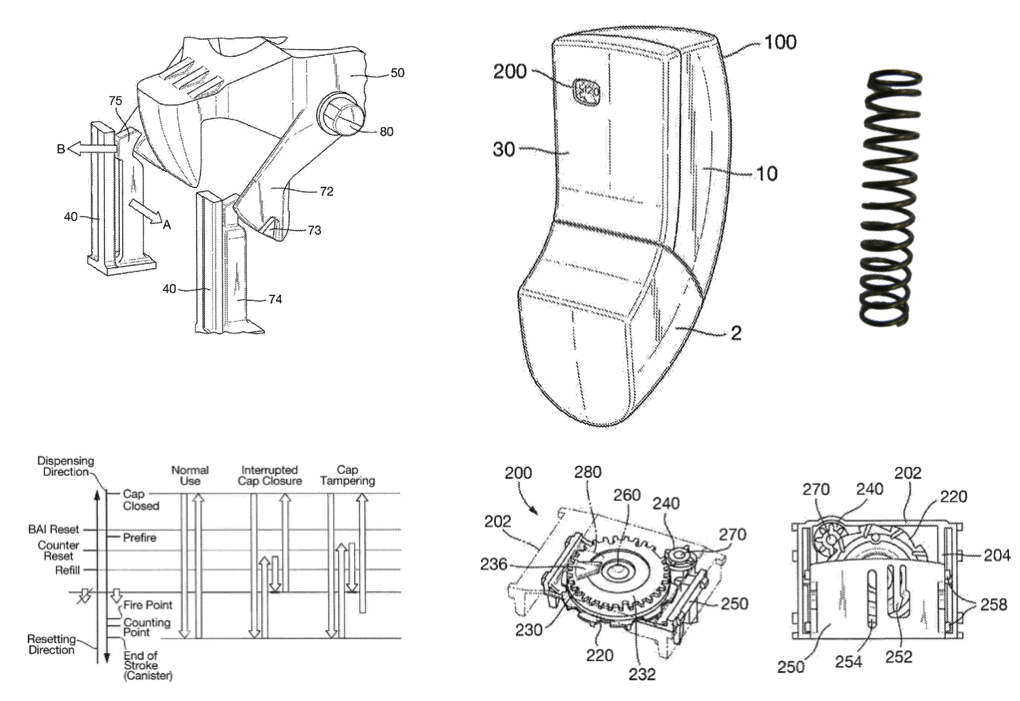
Breath-Activated Inhaler & Counter (7 Years)
The granted Patent WO2013/038169 of Elgaard et al, assigned to Astra Zeneca describes the technology embedded in this novel breath-activated inhaler in detail. UPC’s design contribution is recognised in the inventor list, our role was to provide design and manufacturing leadership.
The decrement counter was front-mounted using two printed wheels to provide the range from 120+ to zero with colour warnings. Linking the short-stroke counter linear motion requirement to the long-stroke pMDI canister drive was overcome in an elegant manner.
Anti-tampering measures from cap ‘abuse’was a key consideration overcome to avoid the possibility of under-counting. The FDA guidelines are clear that a decrement system must provide an accurate indication of doses remaining in the product, to avoid the patient being left without medication.
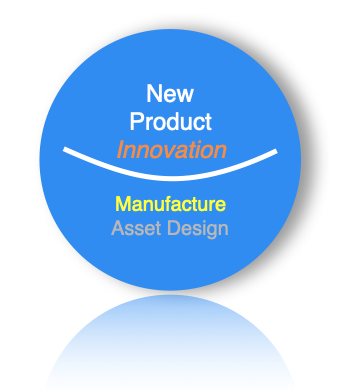
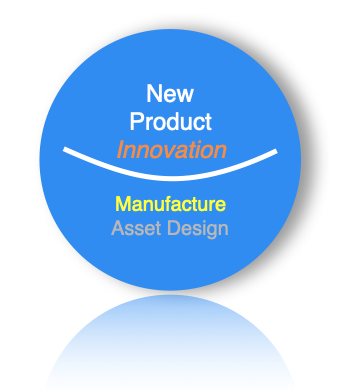
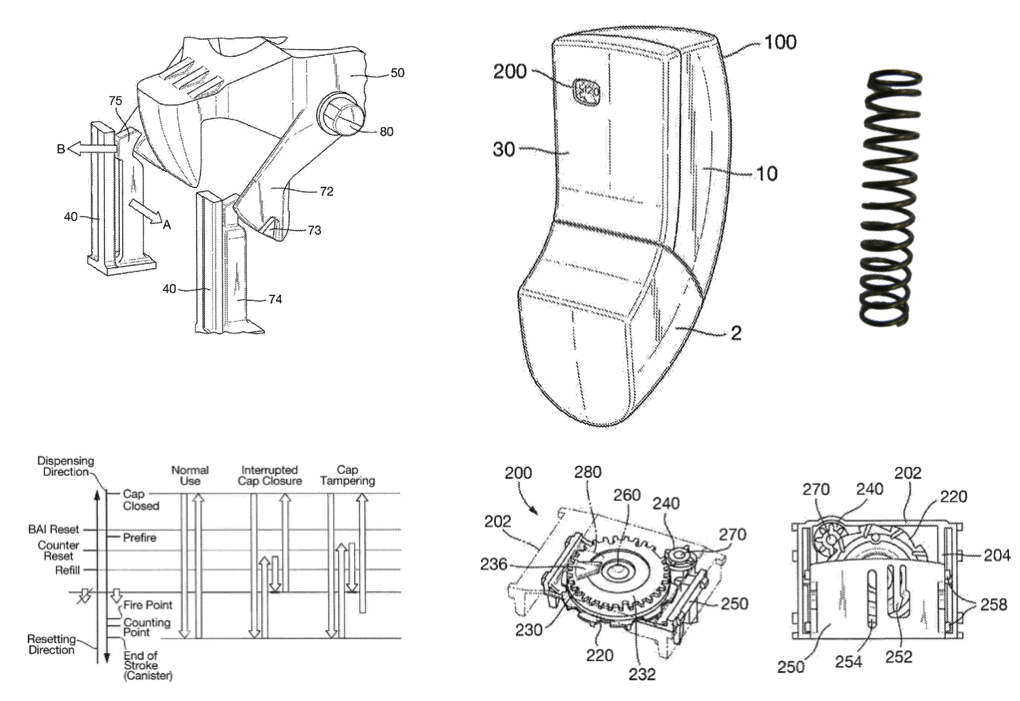
Breath-Activated Inhaler & Counter (7 Years)
The granted Patent WO2013/038169 of Elgaard et al, assigned to Astra Zeneca describes the technology embedded in this novel breath-activated inhaler in detail. UPC’s design contribution is recognised in the inventor list, our role was to provide design and manufacturing leadership.
The decrement counter was front-mounted using two printed wheels to provide the range from 120+ to zero with colour warnings. Linking the short-stroke counter linear motion requirement to the long-stroke pMDI canister drive was overcome in an elegant manner.
Anti-tampering measures from cap ‘abuse’was a key consideration overcome to avoid the possibility of under-counting. The FDA guidelines are clear that a decrement system must provide an accurate indication of doses remaining in the product, to avoid the patient being left without medication.
To be an effective leader, the design team must want to follow you.
Project Phoenix’s duration was measured in years rather than months, and UPC’s contribution was in excess of 10,000 man hours with fortnightly trips to Denmark to work with the team there as the design matured.
Leading the Danish design team was challenging at times due to the language barrier. What barrier you may think, as English was the project language? English has roughly ten million words, Danish about one million. Consequently ‘what the British really means’ was often lost in translation. UPC adapted, and learnt how to be direct and simple in Denglish.
Subtle pieces of design innovation with plastic mouldings were achieved including third function tamper evidence of the fascia for example.
Planning was generally most effective using old-school methods of wall mounted post-its! No software barriers and digital camera mobile phones keep the record.
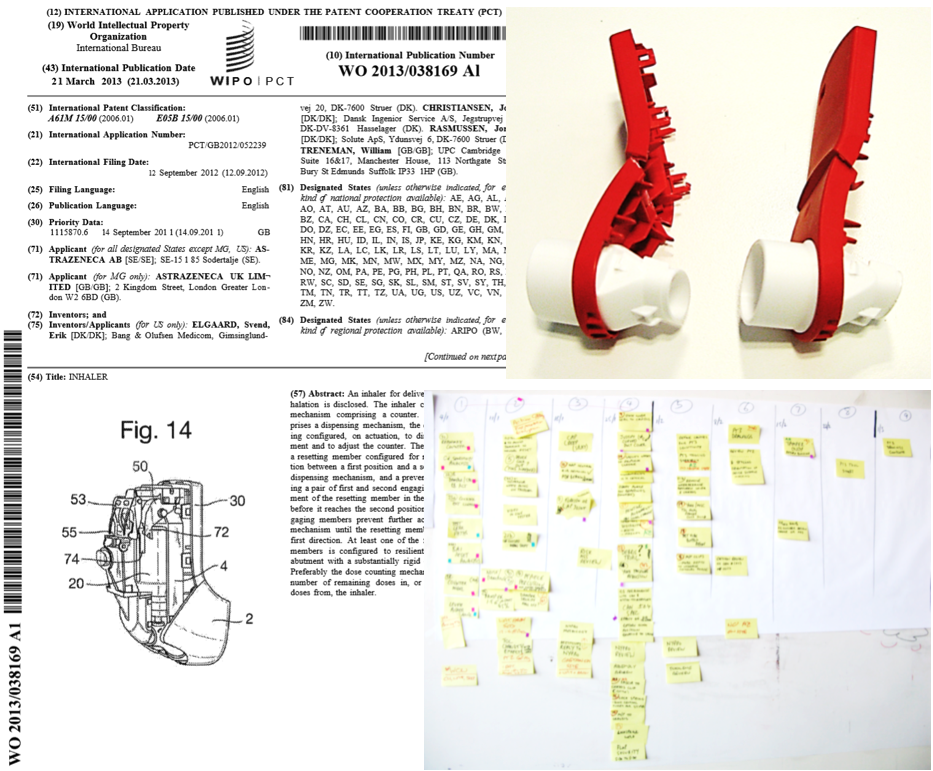
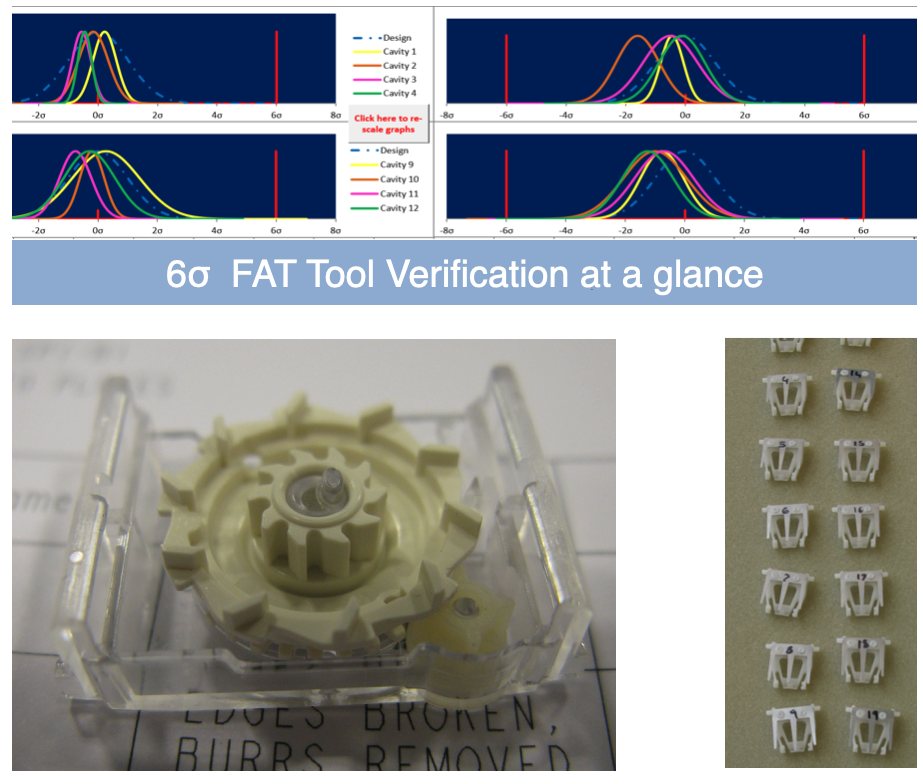
Achieving tool acceptance of a 16 impression set, with a high-capacity assembly cell is challenging.
UPC’s Tool Verification system was used to achieve tool acceptance for the tool suite. Working across four sites using three languages the Tool Verification system visual approach made for rapid understanding and acceptance.
During the design phase UPC’s Unified Model approach was taken to construct a 1000 component dimension input set , driving 100’s of algorithms for all critical to quality performance outputs. The achieved manufacturing mean dimension and sigma was inputted into this predictive model and the in-built traffic light system allowed tool acceptance or change request to be completed the same day as the metrology was delivered.
The traditional ways of tool verification have been eclipsed by linked software systems – such as the UPC approach developed in 2012.