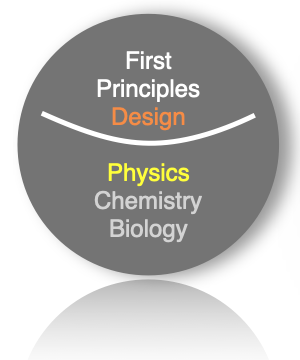
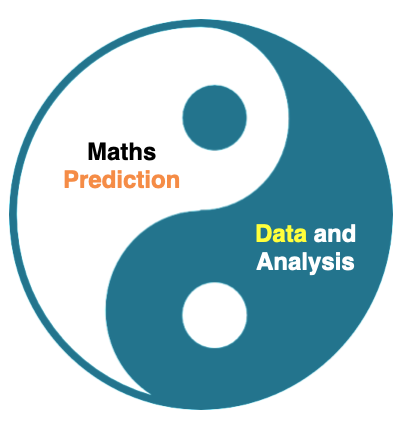
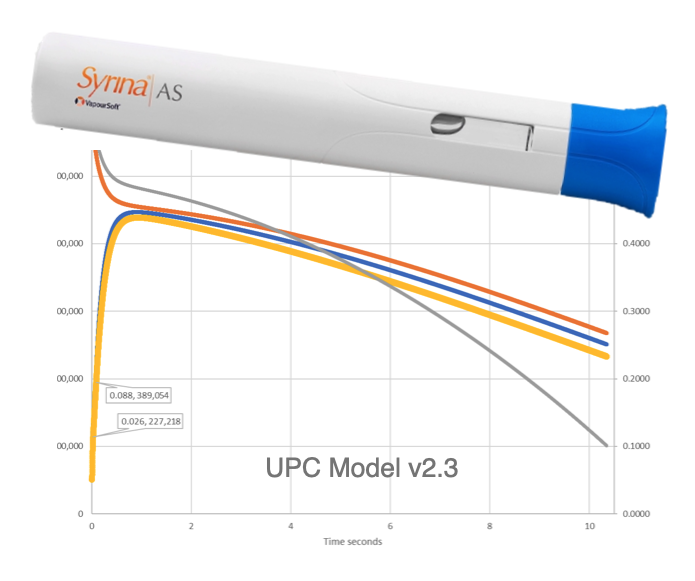
Autoinjector platform
A gas powered novel autoinjector platform had been developed by Recipharm with a maths model that showed the core requirement of pressure build-up with time.
UPC was used to review this model, build a refinement of both the time-stepped approach as well as the direct input average approach to modelling.
The useful output was immediately to identify the key areas requiring control in manufacture as this range of products moved into volume.
UPC also tested various key components on maximum and minimum test pieces for drag force as inputs to the modelling work.
UPC managed to see the ‘wood for the trees’ and provide technical direction for this product range for Recipharm.
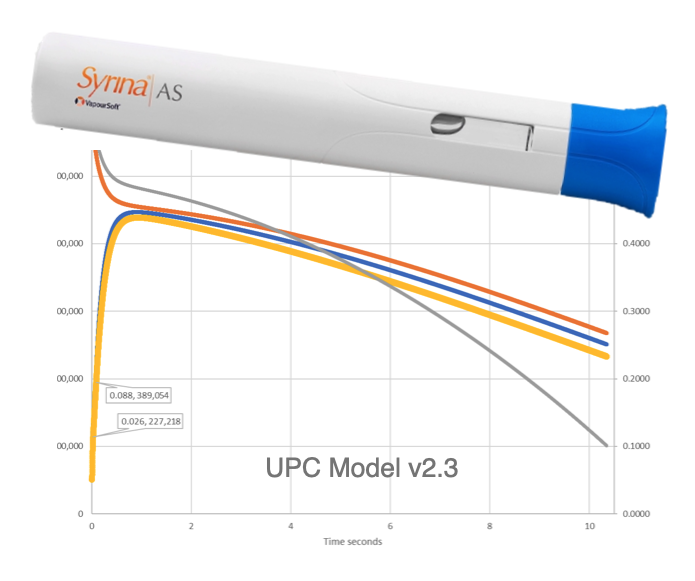
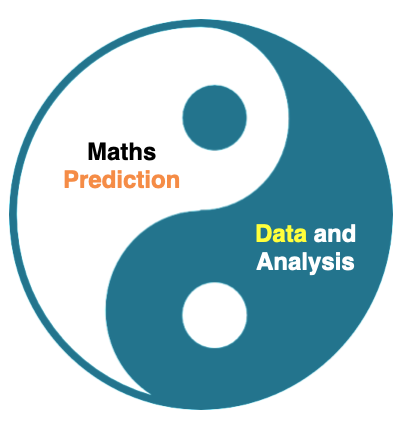
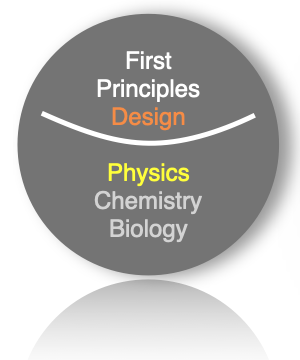
Autoinjector platform
A gas powered novel autoinjector platform had been developed by Recipharm with a maths model that showed the core requirement of pressure build-up with time.
UPC was used to review this model, build a refinement of both the time-stepped approach as well as the direct input average approach to modelling.
The useful output was immediately to identify the key areas requiring control in manufacture as this range of products moved into volume.
UPC also tested various key components on maximum and minimum test pieces for drag force as inputs to the modelling work.
UPC managed to see the ‘wood for the trees’ and provide technical direction for this product range for Recipharm.
Prediction with n=30 Verification - confirmed maths model accuracy
Opposite show the two sides of UPC involved in this project.
On the left is the maths first-principles Physics approach to modelling predictions for the key dimensional inputs.
On the right the laboratory set up used to measure the autoinjector free-air liquid stream timings for the n=30 samples.
This combined approach under one roof ensures the maths is challenged by data.
UPC’s characteristic integrity allows honest refinement of either the physical product or omissions or errors in modelling assumptions corrected. Sometimes work is needed in both areas…
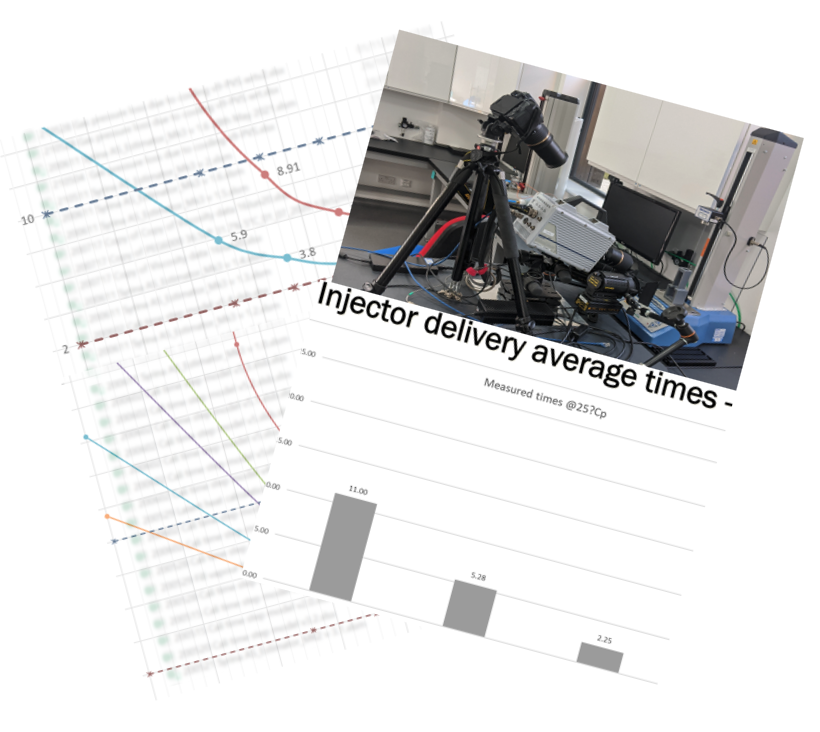
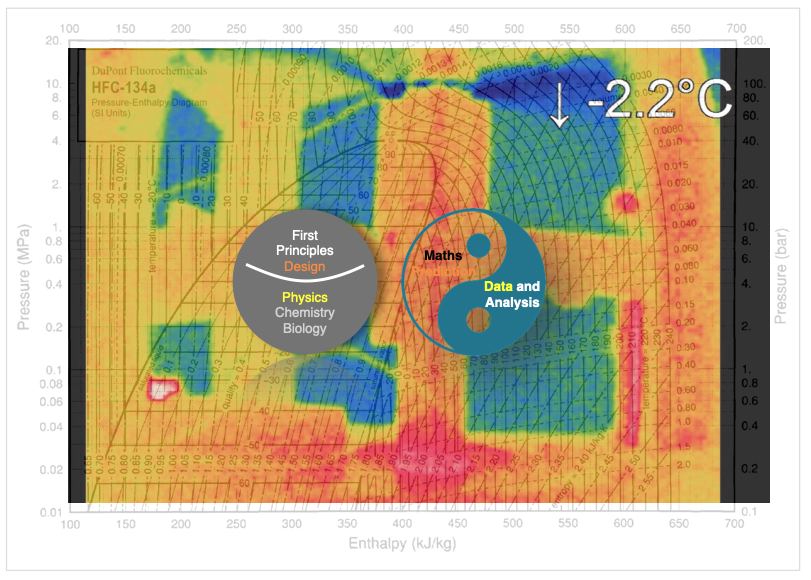
A custom rig logging temperatures, pressures and forces told the full story in colour.
UPC built a truly complex rig that logged 12 channels in real time to build an understanding of how this novel injection system worked.
We also logged the event with high speed video, 125 fps colour digital, as well as 125 fps infrared video. An absolute data fest resulted.
The infra-red image opposite shows a single trial using the PVTF rig with a leak present due to a rig fault. The blue areas showing the cold of the HFA leak to atmosphere.
It was possible to determine the relationship between force and the other factors and so understand how the system worked in detail – what was important, what was not.
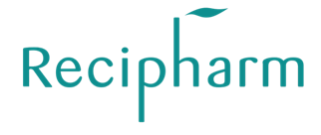